When it comes to metalworking, few processes can rival the precision and versatility of aluminum die casting. It is a fascinating technique that combines the artistry of design with the technical mastery of metal manipulation. In this article, we will take a closer look at the craftsmanship involved in aluminum die casting and explore its unique contributions to various industries.
Aluminum die casting is a method of manufacturing where molten aluminum is injected into a custom-made mold under high pressure. The metal quickly solidifies, taking the shape of the mold and creating intricate, detailed components with exceptional dimensional accuracy. It is a process that has revolutionized the production of complex metal parts and has become an integral part of many industries, including automotive, aerospace, electronics, and more.
One of the key elements that make aluminum die casting an art form is the craftsmanship involved in creating the molds. Skilled toolmakers meticulously craft these molds, taking into account the precise specifications of the desired component. They must possess a deep understanding of geometry, metallurgy, and design principles to ensure the mold's accuracy and longevity. Every contour, every cavity, and every feature is carefully considered and crafted to produce a flawless result.
The process of aluminum die casting itself requires a high level of skill and expertise. The molten aluminum must be carefully controlled in terms of temperature and composition to ensure optimal flow and solidification. The casting machine operators play a critical role in this process, constantly monitoring and adjusting various parameters to achieve the desired outcome. Their knowledge and experience are vital in maintaining the quality and consistency of the cast components.
Beyond the technical aspects, there is an artistic element in the design and finishing of die-cast parts. Designers work closely with engineers to create aesthetically pleasing yet functional components. They consider factors such as texture, color, and surface finish to enhance the visual appeal of the final product. Finishing processes, such as polishing, painting, or anodizing, further showcase the artistry involved in aluminum die casting, transforming raw castings into stunning pieces of craftsmanship.
The versatility of aluminum die casting is another testament to its artistry. It can produce intricate shapes with thin walls, complex geometries, and even integrate multiple components into a single piece. This versatility opens up a world of possibilities for designers and engineers, allowing them to create innovative solutions that were once deemed impossible.
Moreover, aluminum die casting offers numerous advantages over other metalworking processes. It provides excellent strength-to-weight ratios, corrosion resistance, and thermal conductivity. The ability to produce high-quality components at high volumes and relatively low costs makes it an attractive choice for various industries.
In conclusion, aluminum die casting is a remarkable blend of artistry and craftsmanship. From the creation of meticulously crafted molds to the expertise required in the casting process, every step involves skilled professionals pushing the boundaries of what is possible. The result is a range of intricately designed components that are both visually appealing and functionally superior. As technology advances and new techniques emerge, the artistry in metal will continue to evolve, driving innovation across industries and shaping the world we live in.
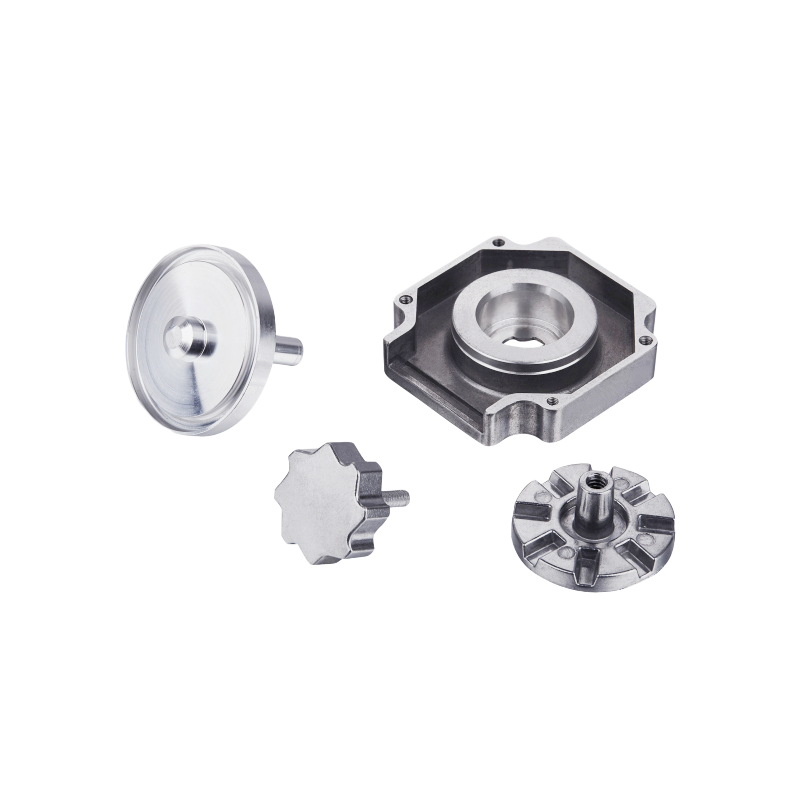
Examples of valve accessories that can be made from aluminum casting technology include: Handles: They are used to manually operate valves and are often made from aluminum to provide a lightweight and corrosion-resistant option. Actuators: They are used to automatically control valves and can be made from aluminum to provide a lightweight and corrosion-resistant option. Couplings: They are used to connect valves to other components in the system and are often made from aluminum to provide a lightweight and corrosion-resistant option. Aluminum casting is a cost-effective process that can produce large quantities of valve accessories with precise dimensions and tight tolerances. The aluminum alloy used in casting is also lightweight and corrosion-resistant, which makes it a suitable choice for valve accessories used in harsh environments or in applications where weight is a concern.