Brass fittings are vital components used in various industries, including plumbing, automotive, and manufacturing. The versatility and durability of brass make it an excellent choice for creating fittings that withstand high-pressure environments and corrosive conditions. However, machining brass fittings requires skill and knowledge to achieve precise results and ensure product quality. In this article, we will delve into the secrets of machining brass fittings like a pro, unveiling essential tips and techniques for achieving outstanding outcomes.
Select the Right Tools and Cutting Parameters:
To
machine brass fittings effectively, it is crucial to have the appropriate tools and cutting parameters. Carbide or high-speed steel (HSS) tools are commonly used for brass machining. Carbide tools offer excellent durability and performance, while HSS tools are more affordable and suitable for less demanding applications. Additionally, using sharp tools is essential to minimize heat buildup and achieve cleaner cuts.
When it comes to cutting parameters, consider a slower cutting speed to prevent overheating and work hardening of the brass material. Start with a conservative feed rate and increase it gradually to find the optimal balance between material removal and surface finish.
Lubrication and Cooling:
Proper lubrication and cooling are essential for successful brass machining. Brass has relatively poor thermal conductivity, making it prone to overheating and work hardening. Applying a suitable coolant or lubricant helps dissipate heat and prolongs tool life. It is recommended to use a water-soluble coolant specifically formulated for brass machining to achieve optimal results. Ensure that the coolant is applied directly to the cutting zone for effective cooling.
Minimize Vibrations:
Vibrations during machining can negatively affect the surface finish and dimensional accuracy of the brass fittings. To minimize vibrations, use appropriate cutting tools with the correct geometries and ensure their stability in the tool holder. Additionally, consider using shorter tool overhangs and rigid setups to reduce the chances of chatter or vibrations.
Maintain Rigorous Quality Control:
Maintaining rigorous quality control throughout the machining process is crucial for producing high-quality brass fittings. Regularly inspect the tools for signs of wear and replace them as needed. Measure the dimensions of the fittings at various stages of the machining process to ensure they meet the required specifications. Implementing a comprehensive quality control system helps identify any issues early on and ensures that the final product meets the desired standards.
Consider Post-Machining Processes:
After machining, brass fittings may require additional post-processing steps to enhance their functionality and appearance. Deburring is often necessary to remove sharp edges and burrs left from the machining process. Depending on the application, fittings may undergo surface treatments such as polishing, plating, or coating to enhance their corrosion resistance or aesthetic appeal.
In conclusion, machining brass fittings to perfection demands expertise, attention to detail, and the implementation of proper techniques. By selecting the right tools, optimizing cutting parameters, ensuring lubrication and cooling, minimizing vibrations, maintaining quality control, considering post-machining processes, you can unlock the secrets of machining brass fittings like a true professional. With dedication and practice, you will achieve exceptional results and deliver high-quality brass fittings that meet the highest standards of performance and reliability.
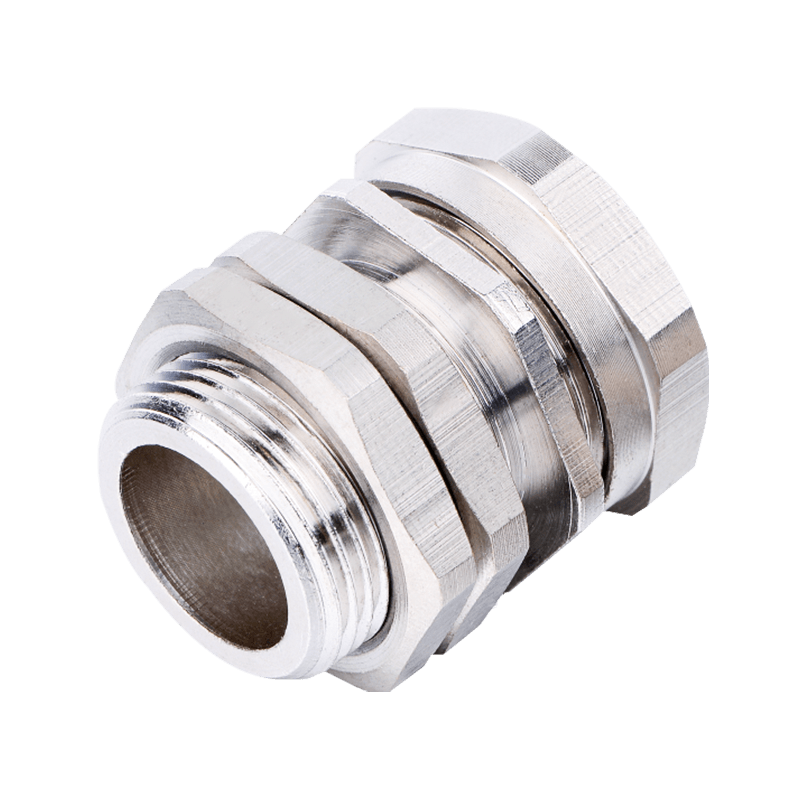
CNC milling is a precise method of machining that uses computer-controlled cutting tools to remove material from the brass fitting. This process can produce precise and accurate fittings with tight tolerances and specific shapes and sizes.Machining brass fittings with nickel plating can be done using various methods, such as CNC milling, turning, drilling, and grinding. The choice of method will depend on the specific design and size of the fitting, as well as the desired level of precision and surface finish.Turning is a method of machining that uses a lathe to rotate the brass fitting and a cutting tool to remove material. This process can be used to create round or cylindrical fittings with a smooth surface finish.